Hidrostatik Yatak ve Şaft Yüzeyine Ni-Al + Cr2O3 Kaplama Uygulaması
“Durmadan Devam Ettiğin Sürece, Ne Kadar Yavaş Gittiğinin Önemi Yoktur” - Konfüçyus
Serkan Özek, Özbek Yelin, Selim Saçma, Buğra Can Şimşek, Veli Karaca
Özet: Hidrostatik yatak, şaftın yükünü desteklemek için ince bir sıvıdan (su, yağ vs) faydalanan, iki eleman arasındaki bir veya birkaç yönde izafi harekete minimum bir sürtünme ile müsade eden fakat kuvvet doğrultusundaki harekete engel olan mekanik bir ekipmandır. Bir akışkan yatak olarak da bilinen hidrostatik yatak, yatağın dış kasası ve desteklediği şaft arasında bir bariyer filmi oluşturmak için harici olarak basınçlı su kaynağı kullanır. Bu çalışmada hidrostatik yatak ve şaft yüzeyinde aşınma, korozyon gibi etkenleri önlemek için yapılmış olan hasarlı Ni-Al-Cr2O3 kaplamanın yüzeyden temizlenerek tekrardan plazma sprey yöntemi ile yenilenmesi ve uygulamanın arıza frekansına etkileri anlatılmaktadır.
Gereksinim
Enerjisa Üretim hidroelektrik santralleri içerisinde hidrostatik yatak teknolojisi 4 Hidroelektrik santralimizde toplam 681 MW kurulu güçteki 10 ünitede kullanılmıştır. Hidrostatik yataklı üniteler, türbin şaftının yükünü desteklemek amacı ile yatak ve şaft arasında bir film tabakasını oluşturmak için nehirden aldığı suyu kullanır. Bu şekilde yataklama faaliyetini yerine getirmek ve sürtünmeyi minimize etmek amacıyla metal şaft ve yatak gövdesi arasında bir kimyasal kullanımdan kaçınılmıştır.
Dünya üzerindeki her malzeme zamanla korozyon sebebiyle veya kullanım ortamına bağlı olarak aşınmaya uğrar. Bu aşınmayı engellemek için ya bulunması ve işlenmesi zor olan özel üretilmiş pahalı malzemeler kullanılır ya da aşınma sonucunda malzeme değişimine gidilir. Türbin şaftı ve hidrostatik yatak sistemi çalışma mantığı ile çevreye duyarlı bir mekanizma oluştururken, bu sistemi meydana getiren şaft ve yatak onarımı ya da değişim yapılması için çok ciddi operasyonel faaliyetlerin gerekli olduğu ekipmanlardır. Bu sistemin hassasiyeti ile suyun metal ekipmanlar üzerindeki aşındırma, korozyon gibi etkileri dikkate alınarak şaft ve yatak gövdesinde seramik kaplama uygulanmıştır.
Kullanılan yataklama yönteminde şaft ve yatak arasında 0.04- 0.08 mm su film tabakasını meydana getirip bunu sürekli kılmak gerekmektedir. Projede yatak ve şaft arasında, yatak boşluğu kullanılan şaft ölçüsüne göre 0.08- 0.14 mm olarak belirtilmiştir. Çalışma ortamından kaynaklanan silt ve kireç birikmesi sebebiyle saha ölçümlerinde 0.05-0.10 mm arasında yatak boşluk değerleri ölçülmektedir. Yataklama değerinde meydana gelen bu düşüş yataklama suyunda düşük debi ve nozullarda yüksek basınç problemine neden olmaktadır. Bu durum çoğu zaman ünite triplerine yol açarak üretim kaybına sebep olmaktadır. Sistem, tedarikçi belgelerinde 10 yıllık bakım periyoduna sahip olmasına rağmen karşılaşılan sorunlar nedeni ile sökülüp görsel kontroller yapılmıştır.
Bu kontrollerde şaft ve yatak yüzeyinde bulunan seramik kaplamanın zarar gördüğü ve yer yer şaft gövdesine kadar korozyonun nüfuz ettiği tespit edilmiştir. Bu tespit üzerine tüm hidrostatik tip yataklamalar kontrol edilmiş ve benzer sorunlar gözlemlenmiştir. Sorunların giderilmesi amacı ile şaft ve yatak sisteminin sökülüp onarımı için yüzeyin tekrar seramik kaplama yapılmasına karar verilmiştir.
Uygulama
Yapılan bu çalışma bir üniversitenin Araştırma ve Uygulama Merkezi desteği ile yerli bir üretim tesisinde uygulanmıştır. Şaft ve yatak yüzeyinde tedarikçi firma tarafından seramik kaplama olarak krom oksit tercih edilmiştir. Yapılan çalışmada malzeme üzerinde bulunan tüm hasarlı kaplama kaldırılıp yeni kaplama tedarikçi verilerine göre termal sprey yöntemi ile tekrarlanmıştır.
Termal sprey kaplama, toz veya tel halindeki kaplama malzemesinin elektrik arkı, alev veya plazma ile ergitilerek, bir püskürtme gazı yardımıyla ergimiş partikülleri altlık malzemeye yapışmasını sağlayan yöntemlerin genel adıdır. Termal sprey kaplamalar korozyon, abrazyon, erozyon, kazıma gibi aşınma olaylarını engellemek, oksidasyonu ve sıcak korozyonu önlemek, ısı yalıtımı, elektrik iletimi veya yalıtımını sağlamak amacıyla kullanılırken yenileme, onarma, final yüzeye sahip ürünün üretimi için de uygulanır. Krom oksit mükemmel aşınma ve sürtünme özellikleri sergiler, bu nedenle bu malzeme plazma püskürtmeli kaplamalarda yaygın olarak kullanılmaktadır.[2]
Uygulama, ekipmanlar üzerindeki eski kaplamanın siyah bazalt cüruf esaslı 24 mesh kum ve 7-8 bar basınç ile yüzeyden sökülüp temizlenmesi ile başlamıştır. Ardından yüzey üzerindeki şaft ve yatak gövdesine ait çelik malzemede çatlak-porozite kontrolü yapılmıştır.
Eski kaplama tabakasının sürülmesi sonrasında iş parçaları yüzeyinde korozyon sonucu oluşan çukurcuk hatalarına rastlanılmıştır. Tüm şaft ve yatak yüzeyi taranarak hasarlı bölgeler ve noktalar belirlenerek işaretlenmiştir (Şekil 1). İş parçasında çatlak, hasar olup olmadığı tespiti için ultrasonik test yapılmıştır. (Şekil 1) Uygulamalar neticesinde herhangi bir mikro veya makro çatlak olmadığı tespit edilmiştir.
Çukurcukların bulunduğu bölgelerde düzgün metal altlığa ulaşıncaya kadar tornalama işlemi yapılmıştır. Ayrıca çalışan iş parçaları yüzeyinden kaplama kalınlığı ölçümleri yapılmıştır (Şekil 2). Yüzeyde kaplama tabakasının inceldiği (yaklaşık 20-25μm) tespit edilmiştir.
Yapılan incelemelerde bağ tabakası ve seal uygulama noktasında eksiklikler olduğu düşüncesi ortaya koyulmuştur. Ön kumlama sonrasında şaftın özellikle kenar kısımlarında korozyona bağlı metal aşınmasının olduğu tespit edilmiştir. İlgili kısımlarda tornalama yöntemi ile 7° açıda ve 20 mm genişliğinde temiz bir bölge elde edilinceye kadar yüzeyden talaş kaldırılmıştır (Şekil 3). Şaft iş parçasının yüzeyinden kaldırılan hasarlı kaplama sonrasında, şaft yüzeyinde de derinliği 1-1.5 mm'ye olan hasarlı bölgeler ekstra olarak tornalanmıştır.
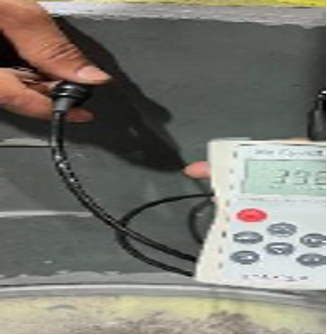
Şekil 2 Yatak Kaplama Kalınlık Ölçümü
Tornalama sonrası iş parçaları özel kumlama odasında yeni kumlama malzemesi kullanılarak manuel olarak kumlanmıştır. Kumlama sonrası tüm yüzeyin SA 2-3 yüzey (parlak yüzey) kalitesi elde edilmesi sağlanmıştır (Şekil 3). Kumlama öncesi, iş parçalarının belirli bölgeleri kumlama bandı ile maskelenmiş, diğer bölgeler için koruma sağlanmıştır.
Kaplama operasyonuna geçilmeden önce iş parçası, döndürme tezgahına bağlanarak salgısız bir dönme sergilediği gözlemlenmiştir. Salgısız dönme homojen kaplama kalınlığının eldesi açısından önemlidir. (Şekil 3)
Hidrostatik yatak kaplamalarının üretiminde Atmosferik Plazma Sprey (APS) yöntemi kullanılmıştır. Dış bir firmanın ürünü olup, 40kW’lik bir güce sahiptir. Uygulamaya maniplator sistemi kullanılarak gerçekleştirilmiş olup, parça 10 dev/dak dönme hızında kaplanmıştır.
APS yöntemi Ar-H₂ (80/15) plazması olup, 9MB püskürtme tabancası seçilmiştir. Püskürtme parametreleri olarak; 500 Amper 80 Voltluk bir enerji kullanılmıştır. Püskürtme mesafesi krom oksit için 67 mm, Ni-Al kaplaması için 100-120 mm olarak belirlenmiştir. Kullanılan kaplama tozları; bağ tabakası için Amdry 956 (Ni-Al) üst yüzey seramik kaplama tabakası için Metco 6156 (-35+15 μm) krom oksit tozu kullanılmıştır. Kaplama sürecinde öncelikle iş parçaları bağ tabakası ile kaplanmış sonrasında da seramik tabakaya ara vermeden geçilmiştir. Proses 24 saati aşkın bir fiil kaplama uygulamasını kapsamaktadır. [1][3]
Bağ tabakası kaplamasını müteakip ara vermeksizin iş parçaları seramik tabaka ile kaplanmış olup kaplama bitiminde iş parçasının yüzey sıcaklığı 45-60°C iken yüzeye reçine uygulanmıştır. Bu şekilde püskürtülmüş kaplamasının doğası olan mikroboşluklar/poroziteler fenolik esaslı reçine ile doldurulmuş/tıkanmıştır. Bu durum 2-3 kez tekrarlı bir şekilde uygulanmıştır. (Şekil 4). Uygulama ile hidrostatik yatakların korozyon ve erozif aşınma dirençlerinin arttırılması sağlanmıştır.[2]
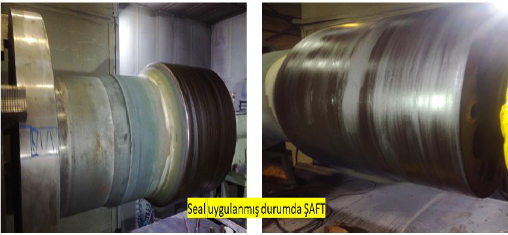
Şekil 4 Fenolik Esaslı Reçine Uygulaması
Yapılan Test Ve Analiz Sonuçları
İş parçaları ile eş zamanlı kaplanan test kuponları; iç yapı incelemesi, yapışma mukavemeti, eğme testi ve sertlik ölçümü işlemlerine tabi tutulmuştur.
Kaplamaların mikroyapı incelemesinde; kullanılan ürün tozunnun püskürtülmesi ile üretilen Bağ Tabakasının üst yüzey elektron mikroskobu görüntüleri incelenmiştir.
Bağ tabakasının üst yüzeyinin elektron mikroskobu görüntüleri Şekil 5'de görülmektedir. Üst yapının genel ve detay incelemesinde; yüzeyde herhangi bir homojensizlik, çatlak ve dökülme benzeri bir kusur gözlemlenmemiştir. Yüksek büyütmede ise Ni-Al toz partiküllerinin plazma alevi içerisinde tamamen ergitilerek yüzeye ulaştığı ve yüzeyi kapladığı görülmektedir. Bağ tabakası uygulaması prensip itibarıyla başarılı bulunmuştur. [4]
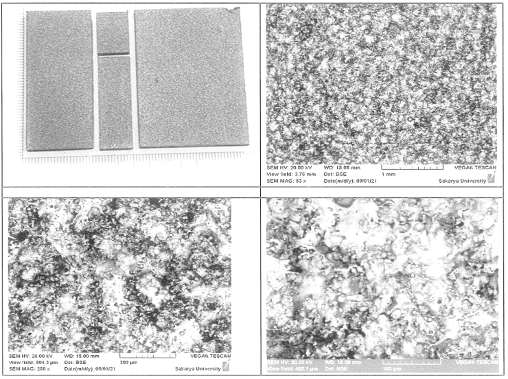
Şekil 5 Bağ Tabakası Yüzeyinin Mikroskop Altındaki Görüntüsü
Krom oksit tozunun spreyle püskürtme sonrasında elde edilen seramik tabakanın üst yüzey görüntüleri incelendiğinde; üst yüzey çatlaksız ve boşluksuzdur, yüzeyde heterojen bir yapı söz konusu değildir, seramik toz partikülleri plazma hücresi içerisinde başarıyla ergitilmiştir.
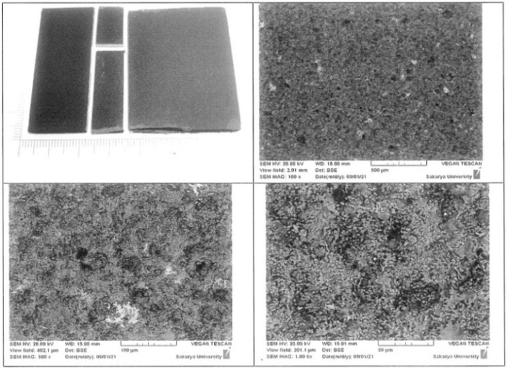
Şekil 6 Seramik Yüzey Mikroskop İncelemesi
İş parçaları kaplamaların kesit mikroskop incelemelerinde (SEM), kaplama kalınlığı ölçülmüş ve bağ tabakası ve bağ tabakası-seramik katman arasında iyi bir yapışma gerçekleştiği görüşmüştür.
Kaplamaların diğer mekanik testleri olan yapışma ve mikrosertlik ölçümleri yapılmış ve sonuçlar literatür değerleri ile karşılaştırılmıştır. Kaplamaların yapışma mukavemeti ASTM 633-1 standardında belirtilen alın yapışma-çekme test yöntemi ile yapılmıştır.
Kaplamaların adhezyon davranışını ortaya koymak amacıyla 2x50x90 mm ölçülerindeki plakalara 3 nokta eğme testi yapılmış ve 270º'lik eğme açısında bükme/deformasyon bölgelerinden herhangi bir dökülme ve lokal atmaya rastlanılmamıştır.
Kaplamaların yüzey sertlik ölçümleri Shimadzu mikrosertlik cihazında yapılmış olup, 300 gr yük ve 20 sn bekleme süresinde oda sıcaklığında gerçekleştirilmiştir.
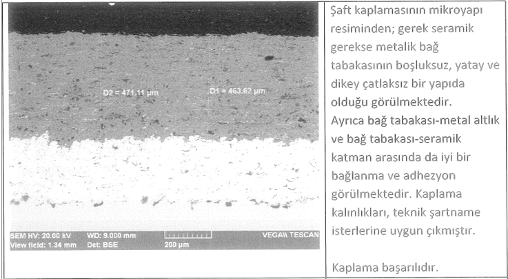
Şekil 7 Mikroskop Altında Kaplama ve Bağ Tabakası Yapışma ve Kalınlık Kontrolü
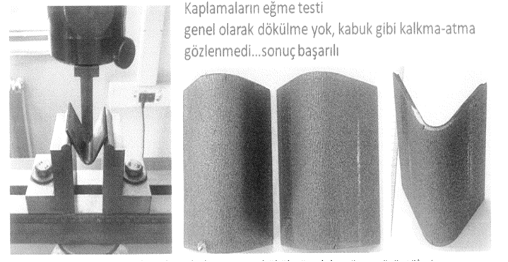
Şekil 8 Alın Yapışma-Çekme Testi
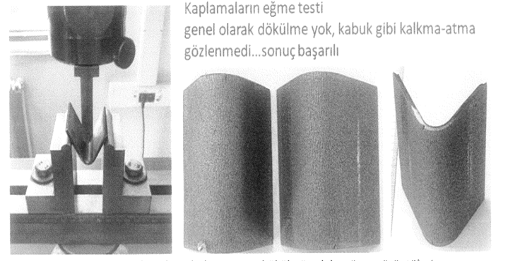
Şekil 9 Numune Eğme Testi
Sonuçlar
Yapılan hidrostatik yatak şaftın Ni-Al ve Cr2O3 kaplaması tamir-bakım süreci prosedürlere uygun olarak gerçekleştirilmiştir. Yatak ve şaft arasında 150-170 mikron arasında radyal boşluk oluşacak şekilde final ölçüler ayarlanmış ve yatak boşluk değeri artmasına bağlı olarak yatak boşluğundan geçen suyun debisi yükselmiş ve nozzle basınçları azalmıştır. Tüm test süreçlerinin dışında ünitenin onarım ve devreye alınmasından tam iki yıl sonra sistem açılarak kontrol edilmiş ve ilk günkü gibi durumunu koruduğu tespit edilmiştir. Kaplamadaki hasarın daha fazla büyümeden ve şaftın ana malzemesine ulaşmadan müdahale edilmesi karşılaşılabilecek daha büyük problemlerin önüne geçmesini sağlamıştır. Bu tespit üzerine hasarlı tüm şaft yatak sistemlerinin yerli ekip ile onarımına karar verilmiştir. Başarılı olarak tamamlanan uygulama ile çok ciddi bir know-how kazanıldığı gibi maddi olarak ciddi bir kazanç sağlanmıştır.
Grafik 1 ve Grafik 2’de sırası ile bir HES santralimizde Ünite-1(U1) & Ünite-2(U2) Hidrostatik Yatak Arıza Başlangıç Zaman, Tamirat Süresi, Arıza Arası Süre verileri görselleştirilmiştir. Balon büyüklükleri (MTTR ) ortalama onarım süresi, yatay eksen arıza başlangıç zamanı, dikey eksen ( MTBF ) arıza arası süredir. Yeşil çizgi bakımın yapıldığı tarihi göstermektedir.
Bakım öncesi dört yıllık veriler incelendiğinde, hidrostatik yatak arızası analizinde U1 için 14 adet arıza kaynaklı duruş yaşanmıştır. Uygulama sonrasında ise 25.08.2022 tarihinde yapılan incelemeye göre U1’de hidrostatik yatak kaynaklı arıza kaydı bulunmamaktadır.
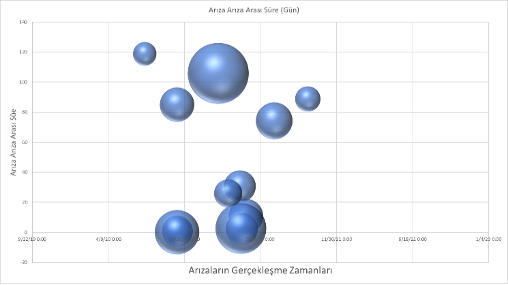
Grafik 1 U1 Hidrostatik Yatak Arıza İstatiksel Veriler

Grafik 2 U2 Hidrostatik Yatak Arıza İstatiksel Veriler
Bakım öncesi dört yıllık veriler incelendiğinde, hidrostatik yatak arızası analizinde U2 için 38 adet arıza kaynaklı duruş yaşanmıştır. Uygulama sonrasında ise 25.08.2022 tarihinde yapılan incelemeye göre U2’de hidrostatik yatak kaynaklı bir adet arıza bildirimi olmuştur. Yeşil çizgi bakımın yapıldığı tarihi göstermektedir.
Durum bazlı bakım sistematiği çerçevesinde yapılan güvenilirlik çalışması kapsamında uygulama öncesi eldeki kayıtlar ve sonrası elde edilen veriler incelenmiştir. gerçekleştirilen uygulama ile elde edilen esas kazanç, ilerleyen dönemde emreamadelik problemi ve tamir maliyeti yaşatabilecek olası yatak hasarlarının önüne geçilmesidir. Bunun yanında potansiyel üretim kayıpları engellenmeştir.
Referanslar
[1] KAYA, Ö. A., ÇAKIR, K., & BOZKURT, Y. (2017). Plazma Püskürtme Yöntemiyle Çelik Levha Üzerine Farklı Alaşımların Kaplanması. Uluslararası Mühendislik Araştırma ve Geliştirme Dergisi, 9(3), 36-42.
[2] ALTUNCU, E., & ÜSTEL, F. (2017). Termal Sprey Kaplama Sektöründe Son Gelişmeler-2017.
[3] Cellard, A., Garnier, V., Fantozzi, G., Baret, G., & Fort, P. (2009). Wear resistance of chromium oxide nanostructured coatings. Ceramics International, 35(2), 913-916.
[4] Minisker, M. A. (2009). Termal sprey yöntemiyle oluşturulan kaplamaların mekanik özelliklerinin incelenmesi (Doctoral dissertation, Fen Bilimleri Enstitüsü).
[5] Li, C. L., Zhao, H. X., Matsumura, M., Takahashi, T., Asahara, M., & Yamaguchi, H. (2000). The effect of NiCr intermediate layer on corrosion behavior of Cr2O3 ceramic coated materials. surface and coatings technology, 124(1), 53-60.
[6] Moubray, J. (2001). Reliability-centered maintenance. Industrial Press Inc.